Steam and Condensate
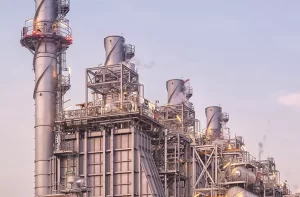
Carryover of excess impurities from the boiler can cause significant downstream problems. In units equipped with steam turbines, contaminant ingress may potentially lead to catastrophic conditions such as turbine blade cracking and subsequent failure.
Even with proper chemistry control, a variety of mechanical factors may influence boiler and steam system conditions, including:
- Fluctuations in the boiler water level, which can either expose tubes to overheating or overwhelm steam separators and introduce contaminants.
- Failure of a water/steam separator in the drum that allows excess moisture to enter the steam system.
- Introduction of impurities directly to the steam via the attemperator system.
In low-pressure boilers, mechanical carryover (the entrainment of water in the steam) can be caused by a high concentration of dissolved solids in the boiler water, resulting in surface tension reduction and boiler water destabilization, and potential foaming in the steam drum. Transported impurities may deposit on superheater tubes, causing tube failures. ChemTreat experts can assist plant personnel in evaluating these conditions, and subsequently provide defoaming chemicals and technical procedures to address carryover issues. Our field representatives can perform tests to determine boiler steam purity, evaluate the system operation, and customize a solution to eliminate carryover.
In many industrial plants, steam passes through numerous heat exchangers, with a varying amount of the exhaust steam recovered as condensate. This condensate may accumulate numerous impurities in the process. A very common impurity is carbon dioxide, which converts to carbonic acid in the condensate, lowers the condensate pH, and corrodes metals. If left untreated, acidic condensate will corrode lengths of condensate return piping, pipe threads, nipples, and elbows, resulting in leaks and process equipment deterioration and failure. ChemTreat personnel can provide expertise on proper corrosion inhibitors and neutralizing/filming chemicals to protect condensate return systems.
Many other impurities may infiltrate condensate return. Some of these include:
- Suspended solids, including metal oxides
- Organic compounds, sometimes including oil and grease
- Dissolved mineral salts
These impurities can cause significant problems in steam generators, including corrosion, deposition, and foaming. ChemTreat personnel can advise on treatment methods and equipment to mitigate these issues with custom boiler water treatment programs and chemicals designed to meet your unique system needs.
Steam Generator Layup
Boilers often need to be taken out of service for a variety of reasons, including seasonal shutdowns, temporary lapses in production, maintenance, or annual inspections by the insurance provider. Plant personnel often forget major corrosion will occur in steam generators without proper layup procedures. Not only does corrosion damage piping and other equipment, but the corrosion products also transport to the steam generator during startups and deposit on tube surfaces. This can lead to severe underdeposit corrosion. ChemTreat has expertise in both wet (short-term and extended) and dry layups. Our boiler treatment programs utilize filming amines, and/or moisture-absorbing chemicals and vapor-phase corrosion inhibitors. Contact a ChemTreat field representative to learn how best to lay up your boiler system.
Water/Steam Chemistry Monitoring
Chemistry upsets have been known to cause boiler tube failures within days, sometimes even hours. Thus, continuous, on-line monitoring is vital for protecting steam generators. ChemTreat personnel can provide expert advice on the equipment and sampling points necessary to protect your steam generator from chemistry upsets. Modern analytical equipment can also be configured to operate chemical feed systems to provide precise control of unit chemistry.